
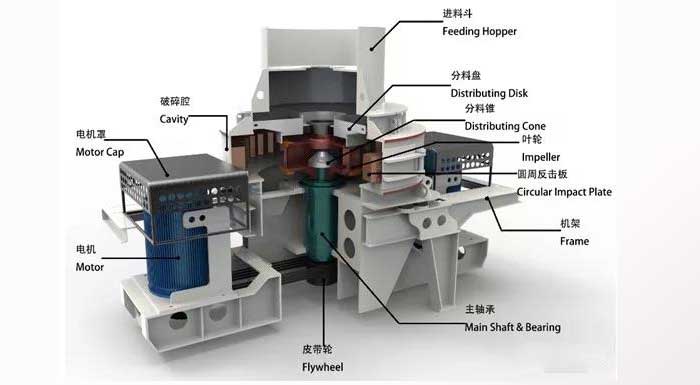
Lelon write in one of their reflow guidelines for electrolytic capacitors to avoid two reflow cycles whenever possible. Termination finishes for applications requiring extended soldering ("DLI offers enhanced magnetic and non-magnetic But they have something in store to counteract the effect, guess you have to pay extra for it.
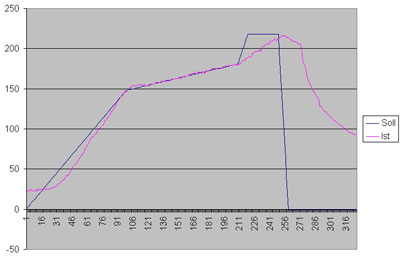
They recommend to reduce the time spent above 230 ☌ to prevent barrier layer thinning. There seems to be an effect on multilayer capacitors (MLC). The strength of this effect is dependent on the paste used. Which is interesting if you think about calibrating the frequency of a device shortly after soldering.Ī research paper on solder joint reliability during multiple reflows indicates that multiple reflows increase the chance of voids forming in the joint and thus decrease the solder joint reliability. This might not be relevant for your board and doing two reflows shortly after the other shouldn't make much difference. if it states the storage temperature prior to reflowing should not exceed 85☌ then this might raise an eyebrow about why and if reflowing the first time should maybe count as being store above that temperature.ĭoing some research indicates some effects which might happen:Ĭrystal oscillators show a decaying frequency deviation after reflow soldering. In the datasheet watch out for any preconditions you might have violated, e.g. In my experience it usually doesn't hurt much, especially if you keep the temperature profile exact. It doesn't seem to make much sense for a manufacturer to specify exactly if a second reflow is possible.
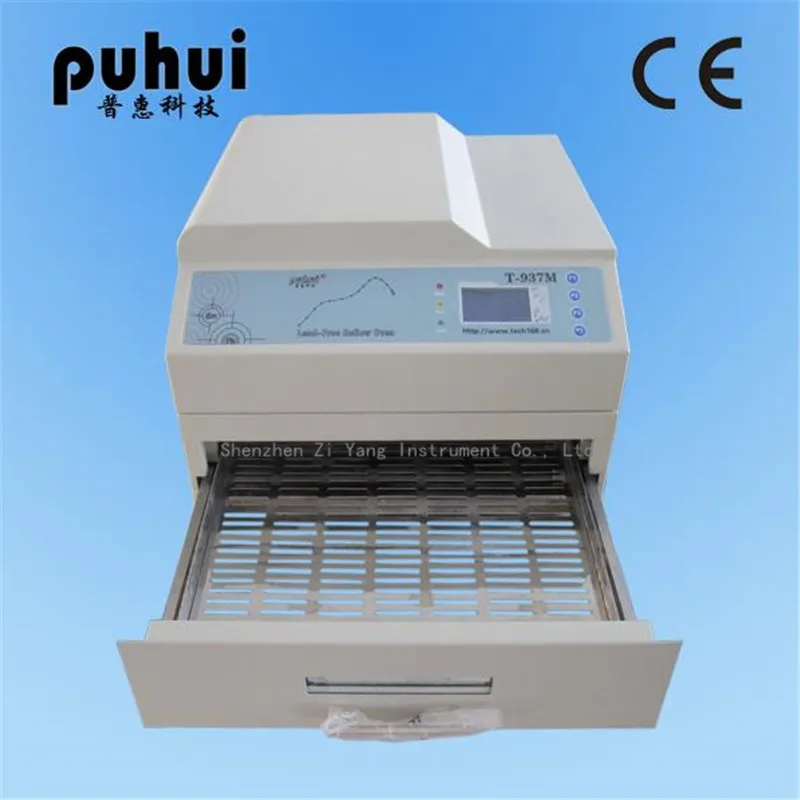
Also the glue used for holding upside down parts may not be designed for a second heating. Parts might be held in place by the solder, so watch out for upside down. Thermal stress during heating (while the part is still held by solid solder) might be too much, especially for MEMS parts and maybe crystals too. Same for other kinds of parts, maybe crystals too.
